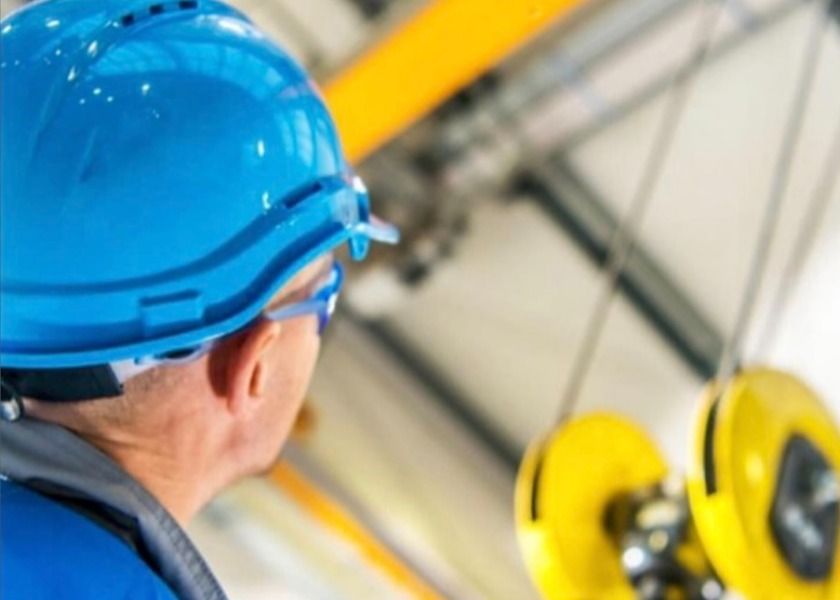
Don’t take the risk: know inspections
Lifting equipment needs to be inspected and maintained to ensure reliability, and safety. Alex Beltrao, Director of Compliance at The Lifting Equipment Engineers Association (LEEA), examines the three levels of inspection for lifting equipment.
Lifting equipment keeps sectors including manufacturing, logistics, ports, maritime, construction, mining, quarrying and renewables operating. Add these to a plethora of non-industrial sectors such as entertainment, medical, aeronautical, agricultural and the military and the ubiquity of lifting equipment is clearly apparent.
Throughout these sectors there will be a variety of cranes, hoists, platforms, cradles and their associated chains, ropes, slings and other tackle that will require pre-use checks, inspection, maintenance and Thorough Examination. Lifting Inspectors and service engineers will ensure the safety and suitability of the equipment used for lifting loads in order to meet regulatory requirements.
All lifting equipment needs to be inspected and maintained, not only to ensure reliability, which will minimise downtime and boost efficiency, but more importantly, to make lifting tasks safe. In any lifting operation, ignorance can all too easily result in severe consequences that can result in an accident, a visit from health and safety inspectors and punishment. Failures are entirely avoidable provided everyone in the chain of responsibility performs their role and understands that lifting equipment has to be looked after.
Inspection of lifting equipment is usually required by legislation. It is the responsibility of the of the relevant competent person to assess the risk and conditions of particular situations and to determine whether all conditions are met to guarantee the safe use of the equipment. Competency is based on practical and theoretical knowledge, experience, training, skill, and behaviour.
Usually, there are three levels of inspection considered and these are described in LEEA’s COPSULE (Code of Practice for the Safe Use of Lifting Equipment). This free to download state-of- the art guide enables lifting equipment users all over the globe and across different industries to meet best practice.
Pre-use inspection
The first level is the pre-use inspection. According to COPSULE 1.2.3.1, this is normally completed by the operator of the equipment before each use and in accordance with the manufacturer’s instructions. It is a basic check for obvious signs of damage. Typically, the operator will be looking for damage such as dents to protective cases, permanent deformations, abnormal noises, presence of and correct marking, or changes in function for example. Any such findings should be reported to the inspection / maintenance personnel.
Interim inspection
The interim inspection, also referred to as frequent inspection, is the second level. According to COPSULE 1.2.3.2, the nature and extent of the inspections is derived from a risk assessment. Interim inspections focus on critical components identified in the risk assessment that may become a danger before the next periodic thorough inspection (examination). The number and frequency of these inspections is also determined by the risk assessment and the manufacturers literature. Interim Inspections are often done at the same time as planned maintenance or following a repair.
Thorough examination
Finally, there is the thorough examination. According to COPSULE 1.2.3, this inspection level may also be called periodic inspection or thorough inspection in different contexts.
It is a visual examination of the lifting equipment carried out by a competent person (usually a third party) carefully and critically and, where appropriate, supplemented by other means such as measurement and testing in order to check whether the equipment is safe to use.
It checks the suitability of the equipment and the inspection / maintenance regime. If a defect affecting the safety of the equipment is found, it suggests there is an issue with the inspection/maintenance regime, the competency of the inspectors or maintainers, the product’s fitness for purpose, etc.
In essence a thorough examination is a safety net, used to identify inadequacies in the inspection/maintenance regime and thereby provide a means of improvement and prevent recurrence. This means that the root cause of any defect found following a thorough examination should be investigated and rectified with appropriate measures to prevent reoccurrence.
Use expert Lifting Inspectors
As a safety organisation with zero accidents and injuries being our prime goal, LEEA wants to remind end users how important it is to use expert Lifting Inspectors who have expertise and high-quality training. Always look for the LEEA logo, whether it is on the in-house Lifting Inspector’s qualifications or an external service provider, because it gives assurance of safe and expert practice when it comes to lifting equipment and services such as inspection.