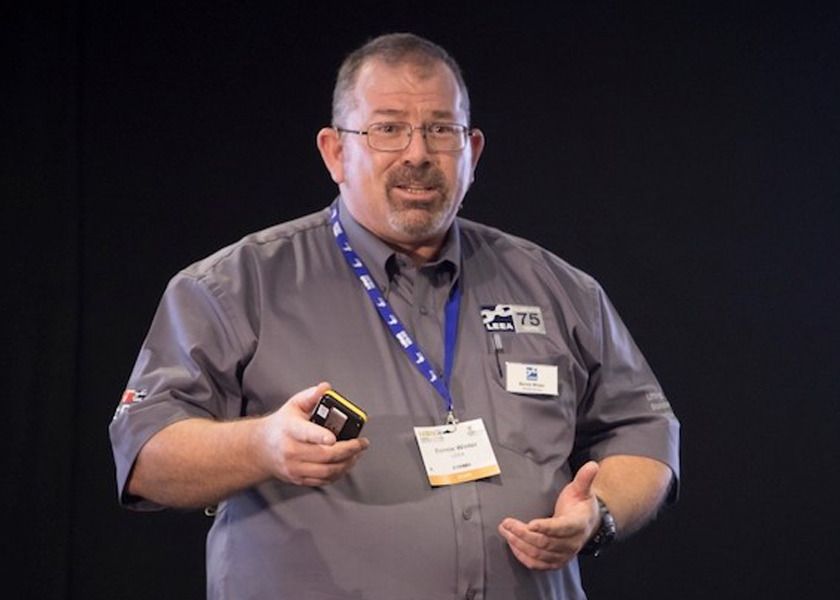
Can Thorough Examination intervals be prolonged?
Bernie Winter of LEEA Technical Services answers a popular question: can the required interval between Thorough Examinations of lifting equipment be prolonged?
LEEA works hard to make guidance more meaningful and effective, helping members to remain compliant, to manage risk, to maintain best practice and ultimately to enhance their know-how. The LEEA Library is an extensive collection of essential documents and resources relating to all aspects of the safety, design, manufacture, testing, examination, servicing, certification and supply of lifting equipment. Access to this expertise has been made substantially easier thanks to the Association’s investment in new technology and multilingual delivery.
One of LEEA’s most popular downloads from this font of knowledge is ‘LEEA 032 – ‘Guidance on Written Schemes of Examination for Lifting Equipment’. Why should this be? Yes, it is a free download, but there’s more to its popularity than that. The true reason is that it addresses the most common topic among the questions received by the LEEA Technical Team, that is regarding the prolonging of required intervals between Thorough Examinations of Lifting Equipment.
One of the misconceptions about Written Schemes is that they can be drawn up as and when it is convenient to do so if, for example, a competent person is unavailable until after the examination inspection due date or a duty holder has missed the examination/inspection due date. This, however, is not the case. Moreover, it should be noted that such a situation would neither be permitted or recognised by the enforcing authorities. What should happen is that the lifting equipment in question be quarantined until it can be examined/inspected by a competent person.
Unfortunately, LEEA has encountered many schemes that have been based on practicalities surrounding the expense and availability of a Competent Examiner. This is wholly unacceptable and is often considered as putting profit before safety.
Another common misconception is that a Written Scheme can be used for lifting accessories. While in theory this may be possible, the truth is that in most cases it is not suitable. There are two problems here. The first is that usage is difficult to measure and that is normally the basis for examination schemes. Secondly, lifting accessories can be accidentally damaged every time they are used – and even when they are not in use. This should be picked up during pre-use checks, but unfortunately, often it is not, and 6 months is the accepted interval between thorough examinations/inspections as a result.
It is important to remember that, where legislation allows, before a Written Scheme can be drawn up, a rigorous risk assessment is carried out on the equipment. Information for best practice to cover the basics in this area can also be found in the Lifting Operations and Lifting Equipment Regulations 1998 (LOLER) Approved Code of Practice (ACOP) & Guidance to Reg 9(3)(a)(iii). LOLER is freely available online and used in many areas around the world. We would also suggest taking the following crucial points into consideration: the condition of the equipment; the environment in which it is to be used; and the number and nature of lifting operations and the loads lifted. These are expanded on in more detail in LEEA 032. Once management has satisfied themselves that a Written Scheme is suitable based on this risk assessment, then they may have this drawn up by a competent person.
For those wishing to learn more about this subject, we would certainly encourage further reading of LEEA-032. In addition we’d suggest looking at LOLER 1998 (Paragraphs 330–345), LEEA-065-‘Guidance to hire companies and examination schemes’, LEEA-069-1-‘Guidance to Written Schemes of Examination for Stainless Steel Submersible Pump Lifting Chain and Accessories’ and, finally, on the Frequently Asked Questions at leeaint.com, seek out FAQ M01 – ‘Can the written scheme of examination option in LOLER be used for lifting accessories?’ For those involved in lifting operations, this knowledge is not only help to ensure they are compliant and working according to best practice but, crucially, that they are working in safety.